Currently, Titania participates in collaborative innovation projects at both national and European level, within the scope of its lines of research.
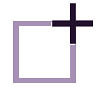
Lines of research
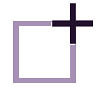
Capabilities
Our capabilities allow us to participate in low TRL basic research projects, oriented to the development of materials with advanced properties or to the improvement of processes. At the same time, we participate in higher TRL projects, closer to the market.
We make the existing capacities of our testing laboratories available for the development of R&D projects. This allows us to participate with the guarantee provided by the accreditations and certifications of each of these laboratories.
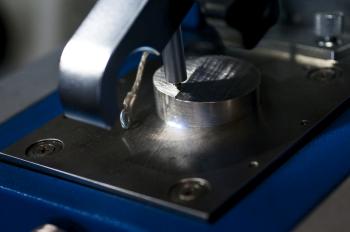
Chemical Analysis
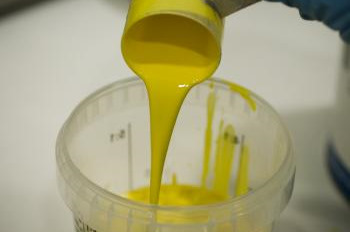
Physicochemicals
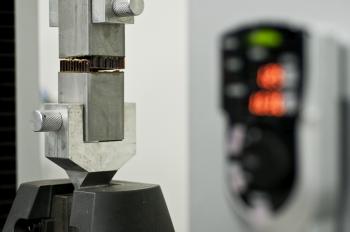
Mechanical Tests
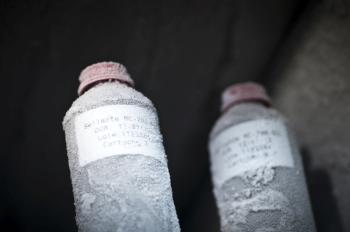
Climate Tests
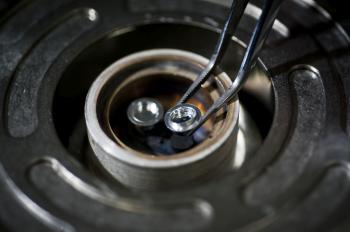
Thermal Analysis
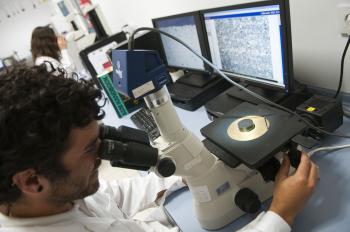
Microscopy
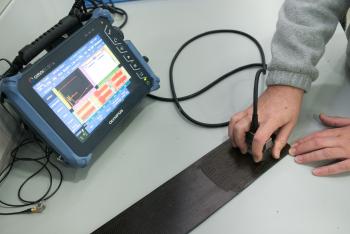
Non-destructive
Surface treatments
- 13 baths with a capacity of 150 litres
- Tartaric-sulphuric anodising (TSA)
- Phosphoric acid anodising (PAA)
- Sulphuric acid anodising (SAA)
- Degreasing and pickling
- Chemical conversion layers (CCC)
- Sealing
- Paint booth
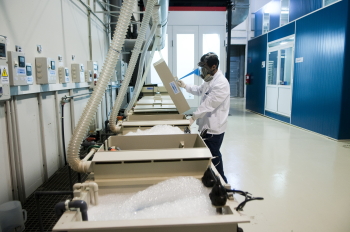
Composite manufacturing
- Autoclave with a diameter of 1.0 m and a length of 1.5 m, which permits working with up to 180 and 150 bars in N2 atmosphere.
- Clean room.
- Refrigerated room.
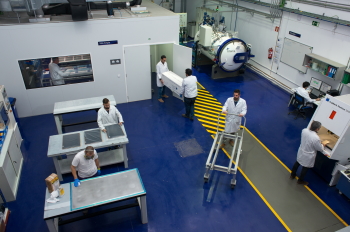
The participation of the University of Cádiz as a PRB allows us to incorporate the most advanced characterisation techniques in our projects, complementing those that exist in our laboratories
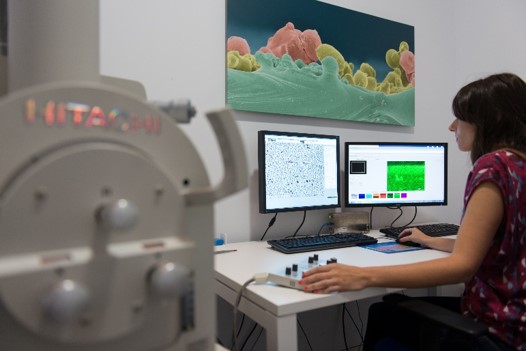
SEM
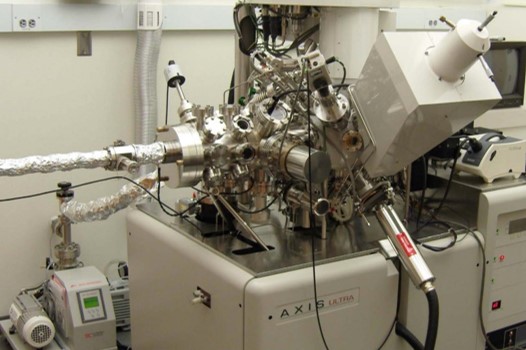
XPS
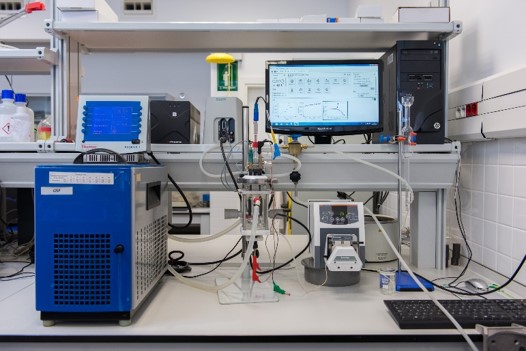
Electrochemical techniques
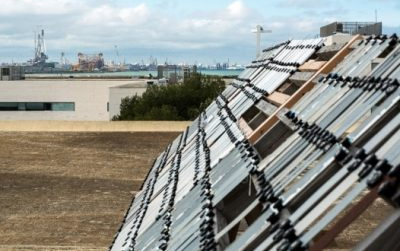
Atmospheric corrosion
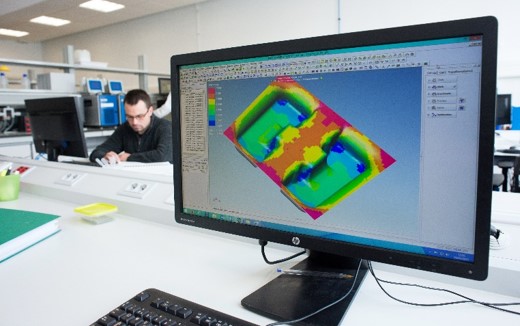
Simulation
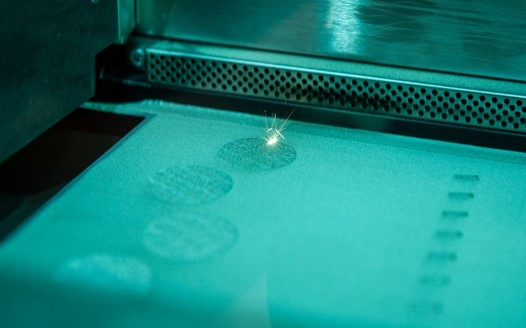
Additive manufacturing
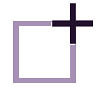
Technology partners
We participate in projects led by the main players in the aerospace sector, and other sectors, as a support center for their R&D departments.

Contact with our expert
Pedro Astola
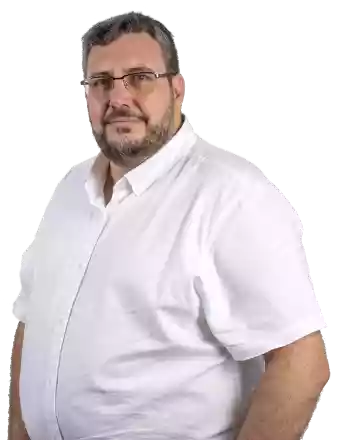